In the baking and catering industry, cream chargers are essential for quickly whipping cream. However, like any equipment, they can encounter various issues during use. Understanding these common faults and their solutions ensures smooth operation and user safety. This article delves into the basic principles, common faults, and corresponding solutions for cream chargers.
Common faults include operational errors, material incompatibility, and extreme environmental impacts. Operational errors, such as incorrect installation angles or repeated puncturing, can lead to insufficient gas release or equipment damage. Material incompatibility, like seal corrosion or electrochemical corrosion between different materials, can cause leaks. Extreme temperatures can affect gas release efficiency. To avoid issues, proper installation, suitable materials, and maintaining optimal environmental temperatures are essential, along with regular pressure monitoring and eco-friendly recycling.
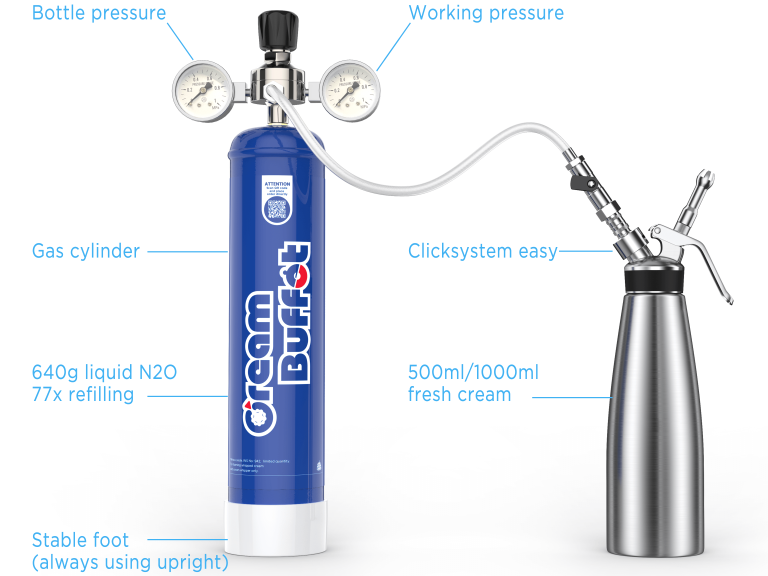
1. Basic Principles and Structure
1.1 Mechanism
Cream chargers work based on the properties of high-pressure N₂O (nitrous oxide). At room temperature and pressure, N₂O is gaseous but liquefies under high pressure. When liquid N₂O is injected into cream, it rapidly gasifies into tiny bubbles upon pressure release. These bubbles evenly disperse in the cream, causing it to expand and become fluffy, achieving quick whipping.
The cylinder is made of high-strength metal, typically aluminum alloy or special alloy steel, leveraging its excellent pressure and fatigue resistance to ensure structural stability during filling and use, even under high pressure, preventing cylinder rupture and other safety incidents. The top seal valve uses a special puncture seal design, which only releases gas when pierced by a dedicated pin, initiating the whipping process. This design effectively prevents accidental gas leaks.
1.2 Key Components
- Cylinder: Usually made of pressure-resistant aluminum or steel containers to store liquid N₂O. Aluminum cylinders are lightweight, cost-effective, and form a dense aluminum oxide protective layer, enhancing corrosion resistance. Steel cylinders offer higher strength and toughness, suitable for high-safety applications. Regardless of material, manufacturing processes like forging and heat treatment ensure the cylinder can withstand internal pressures up to 8.2 bar or higher, ensuring safe gas storage.
- Seal Valve: Designed as a one-way valve, its internal valve core is typically made of rubber or engineering plastic. These materials provide good flexibility and sealing. When gas is released, the valve core opens under pressure; otherwise, it remains tightly closed, ensuring gas is only released during use, preventing leaks and ensuring safety.
- Safety Membrane: Made of metal foil or composite materials with specific thickness and strength. If internal pressure exceeds safe limits due to high temperature or overfilling, the membrane ruptures at a preset pressure, rapidly releasing pressure to prevent cylinder explosion. The rupture pressure is precisely calculated and rigorously tested to ensure safety without frequent ruptures from minor pressure fluctuations.
1.3 Compatible Equipment
Cream chargers must match specific whippers. Different whippers have varying pin lengths, interface sizes, and sealing methods. Incorrect matching can lead to insufficient gas release or leaks, wasting gas and posing safety risks. Therefore, always refer to the product manual to ensure compatibility and follow installation and usage guidelines. If you choose Cream Buffet’s cream chargers, we also sell compatible whippers.
2. Operational Errors
2.1 Incorrect Installation Angle
- Symptoms: Tilting the charger causes the pin to partially pierce the seal valve, narrowing the gas release channel. This results in insufficient gas release, leading to poorly whipped cream with a semi-liquid texture, unsuitable for piping or decoration.
- Solution: Install the charger vertically, aligning the pin with the seal valve’s central axis. Gently rotate the charger until a clear “click” is heard, indicating proper installation. Ensure stability during installation to avoid angle deviations.
2.2 Repeated Puncturing
- Symptoms: If the user mistakenly believes the initial puncture failed and forces a second puncture, the precise threads at the charger-whipper interface may wear, reducing connection tightness. The seal may also tear from uneven force, causing gas leaks, which reduce efficiency and pose explosion risks.
- Solution: If the initial puncture doesn’t work, stop immediately and check for compatibility or pin damage. If issues persist, replace the charger. Never attempt a second puncture to avoid damage and safety risks. Dispose of old chargers properly to prevent residual gas hazards.
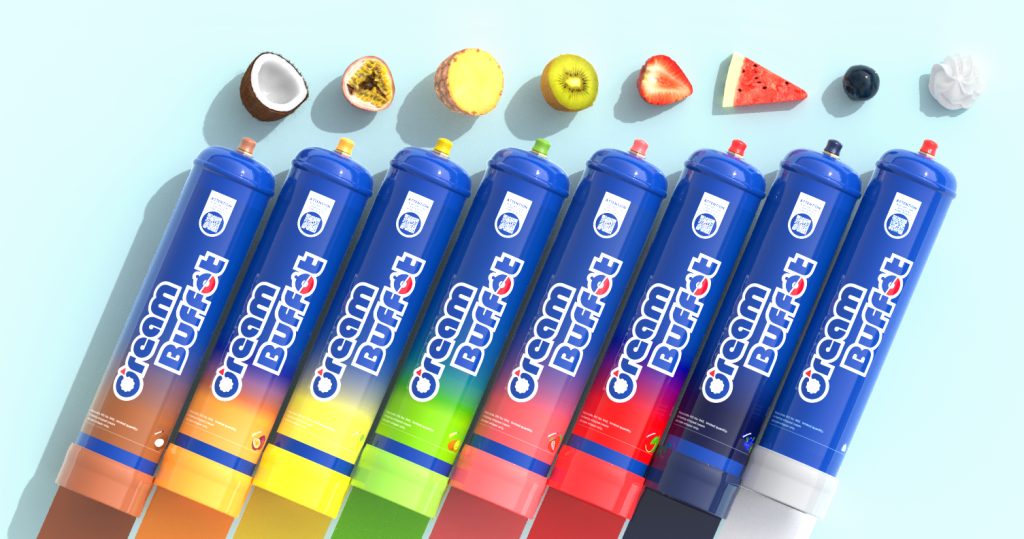
3. Material Compatibility Issues
3.1 Seal Corrosion
- Symptoms: Prolonged exposure to fatty cream residues causes oils to penetrate rubber seals, leading to swelling and oxidation. This hardens the seals, reducing elasticity and sealing performance, causing gas leaks that form mist around the equipment, affecting the environment and reducing efficiency.
- Solution: Clean the whipper interface thoroughly after each use with a dedicated, non-corrosive cleaner. Use food-grade fluorocarbon seals, which resist oil and chemical corrosion, maintaining sealing performance and extending seal life.
3.2 Material Conflict Between Charger and Whipper
- Symptoms: When aluminum chargers contact stainless steel whippers, electrochemical corrosion occurs due to their different electrode potentials in the presence of electrolytes like moisture or cream residues. Aluminum, as the anode, oxidizes, causing corrosion pits and rust at the interface, reducing connection tightness and potentially leading to leaks, shortening equipment lifespan and safety.
- Solution: Prefer matching materials, such as aluminum chargers with aluminum whippers or steel chargers with steel whippers, to reduce corrosion risks. If mismatched materials are unavoidable, apply food-grade lubricant to the interface to form a protective layer, isolating electrolytes and preventing corrosion. Ensure even coverage and regular reapplication.
4. Extreme Environmental Risks
4.1 High Temperatures
- Risk: At temperatures above 50°C, according to the ideal gas law (PV = nRT), N₂O gas expands, increasing internal pressure. If pressure exceeds the safety membrane’s rupture point, the membrane may burst prematurely, causing gas leaks. Leaking high-pressure gas can harm personnel and equipment, and N₂O mixed with air at high temperatures may pose explosion risks.
- Solution: Use insulated packaging like polyurethane foam or aerogel felt during transport to reduce external heat. If you choose Cream Buffet, we provide the safest transport services. Store chargers in cool, well-ventilated areas below 30°C, with temperature monitoring to ensure safety.
4.2 Low Temperatures
- Risk: Below 5°C, N₂O’s liquefaction rate drops, reducing gas solubility in cream. This leads to insufficient gas release, resulting in poorly whipped cream with a hard texture and lack of fluffiness, affecting product quality.
- Solution: Before use, soak the charger in 20-25°C water for 3 minutes to raise N₂O temperature, improving liquefaction and gas release. Never use open flames to heat chargers, as this can cause localized overheating and explosions.
5. Regulations and Safety Certifications
5.1 Compliance Labels
Cream chargers must have DOT (Department of Transportation) certification, which ensures safety and compliance for pressure vessels transported within the U.S. through strict design, manufacturing, and inspection standards.
Notably, Cream Buffet’s cream chargers have DOT, FDA (Food and Drug Administration), TUV (Technischer Überwachungsverein), and ISO (International Organization for Standardization) certifications. FDA certification ensures food contact material safety, TUV reflects high quality and reliability, and ISO demonstrates international quality management standards.
Chargers should also display production batch, expiration date, and filling pressure for traceability, timely use, and safe operation.
5.2 Risks of Illegal Modifications
Refilling chargers with CO₂ or other gases risks inaccurate pressure control due to differing gas properties, potentially causing whipper explosions. Other gases may react with cream, causing contamination, odors, or discoloration, endangering health. Cream chargers are single-use, designed for specific gases and conditions. Modifications violate pressure vessel regulations, void warranties, and may lead to legal consequences.
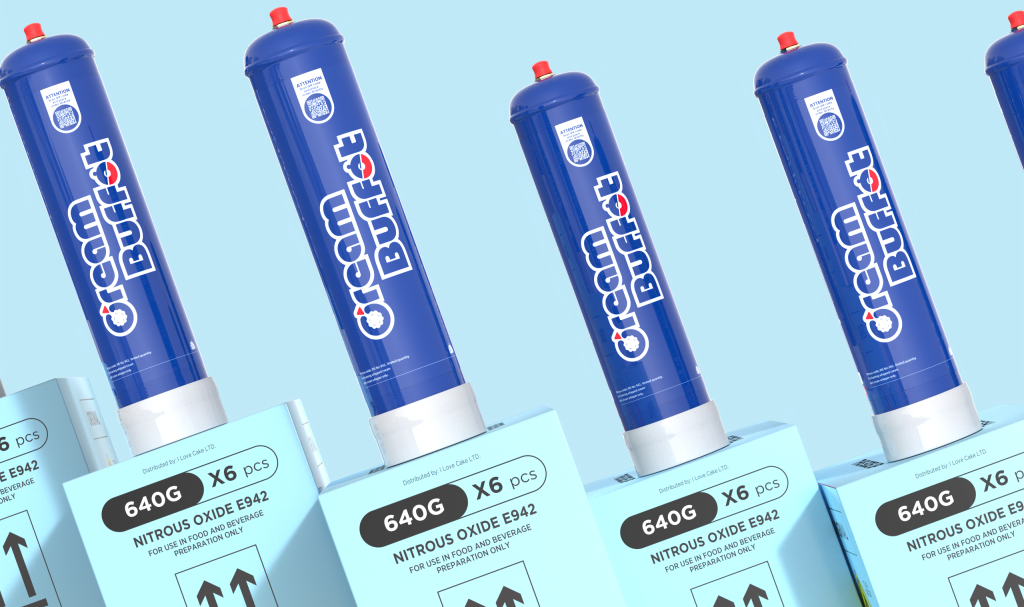
6. Advanced Maintenance Strategies
6.1 Pressure Monitoring
Use digital pressure gauges to regularly check whipper internal pressure, which should be 6-8 bar. Digital gauges offer high accuracy and intuitive readings, helping detect issues like high pressure from overheating or low pressure from leaks. Address anomalies promptly to ensure proper operation.
6.2 Lifespan Prediction
Calculate theoretical usage based on total gas volume (640g) and single-use consumption (1.5-2g). For example, at 2g per use, theoretical usage is 320 times. If actual usage falls below 80% of this, check for leaks from seal aging or loose connections to extend lifespan and improve efficiency.
7. Environmental and Recycling Standards
7.1 Empty Cylinder Disposal
- Confirm no residual pressure by shaking the cylinder; no sound indicates empty.
- Puncture to release gas and recycle through professional agencies with proper equipment for safe dismantling and resource recovery.
- Never dispose of empty cylinders as regular metal waste, as residual gas poses safety risks and hinders recycling.
7.2 Carbon Emission Control
Each cylinder emits ~0.3kg CO₂ during production, mainly from raw material extraction, manufacturing, and energy use. To reduce emissions, choose carbon-neutral brands like Cream Buffet, which use clean energy, optimize production, and participate in carbon offset programs to achieve lifecycle carbon neutrality.
8. Fault Diagnosis Flowchart
Pressure anomaly → Check temperature → Calibrate pressure ↔ Replace charger
↓
Gas leak → Soap water test → Replace seal/charger
↓
Release blockage → Clean puncture pin → Check installation angle
↓
Complete failure → Check expiration date → Submit for manufacturer inspection
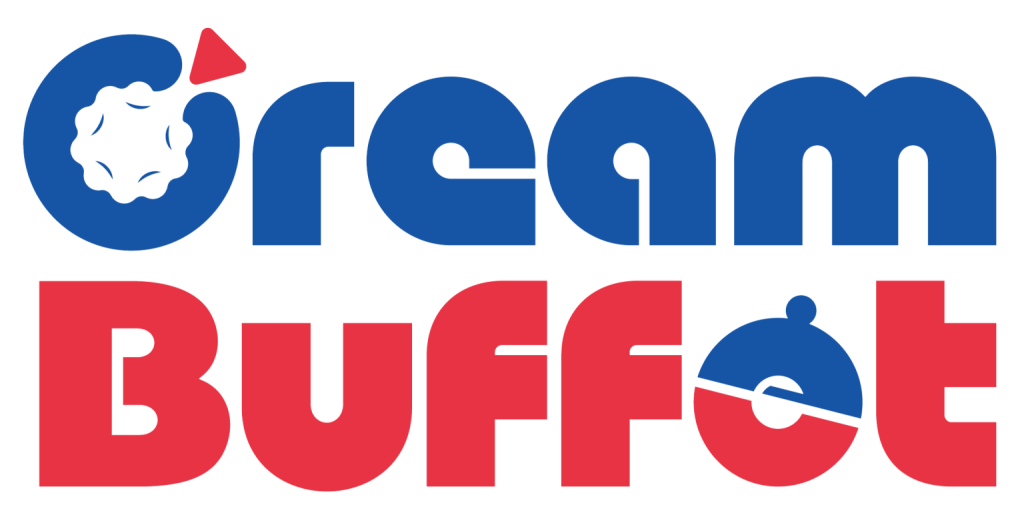
9. Conclusion
By comprehensively understanding cream chargers—from basic principles to advanced maintenance, regulatory compliance, and environmental requirements—we build a complete knowledge system. For any issues, consult Cream Buffet, where our team is available 24/7.
For the best cream chargers and professional service, try Cream Buffet today!